Производство штампованных деталей из металла. Листовая штамповка деталей
Для изготовления плоских и объемных изделий с тонкими стенками используется листовая штамповка деталей. Она реализуется при помощи специальных штампов и прессов или без них. Ее разделяют на горячую и холодную.
Горячий способ обработки применяется для производства днищ котлов, буев, элементов судостроения. Используются заготовки толщиною 3-4 мм. Составляя чертежи для деталей, учитываются видоизменения металла: возможная утяжка при пробивке или гибке. Для минимизации неликвида делаются допуски.
Холодная штамповка более экономична и прогрессивна. Она позволяет делать точные детали, поэтому не требует допусков, а значит лишнего расхода материалов. Ее применяют для изготовления мелких и больших изделий (кузовов автомобилей, шасси, обшивки кораблей, элементы часов и т.д.).
Для штамповки используются такие станки: вибрационные ножницы, кривошипные и гидравлические прессы. В зависимости от типа оборудования различают разделительную и формоизменяющую обработку.
Преимущества нашей компании
- Разноплановые станки. Наш цех оснащен современными, производительными станками. Мы выпускаем партии продукции на штамповочном оборудовании с усилием от 6.3 до 100 тонн;
- Металл в наличии. Мы одинаково работаем с собственным сырьем или материалом заказчика, по его желанию;
- Заказы от 1 единицы. Мы не устанавливаем ограничений. К нам можно обращаться с просьбой изготовить 1 заготовку или целую партию;
- Индивидуальный подход. Наши мастера в точности повторяют характеристики изделий. Для разработки конструкторской документации достаточно эскиза или образца;
- Оперативность. Сроки производства определяются до начала работ. Они зависят от количества деталей, которые нужно сделать;
- Богатый опыт. Мы занимаемся обработкой металла с 1993 года. За это время у нас сформировался надежный штат сотрудников;
- Доступность. У нас удобное расположение. Мы находимся в Москве. Нет необходимости ехать в область.
Стоимость услуг компании
За счет оптимизации цеха мы установили доступные цены на наши услуги. Мы используем высокоточные прессы и штампы, позволяющие обрабатывать большие партии металла за короткий промежуток времени, сохраняя качество.
Листовая штамповка деталей включает расходы на закупку металла, оплату работы мастеров, накладные траты и НДС. Уточнить расценки, определить возможность решения задачи можно с нашим менеджером по телефону или через форму обратной связи.
При использовании материалов заказчика, они в смету не включаются. У нас действуют скидки для постоянных заказчиков.
Этапы сотрудничества
- Фиксация заявки по e-mail или по телефону;
- Рассмотрение возможности реализации задачи менеджером. Он определяет стоимость, сроки и сложность;
- Составление сметы и выставление счета;
- Заключение договора;
- Внесение средств за услугу;
- Запуск производства;
- Сдача продукции клиенту. При выявлении несоответствия технической документации, мы гарантируем оперативную коррекцию изделий.
Листовая штамповка в наши дни активно используется для производства широкой номенклатуры изделий многими промышленными отраслями, имеющими отношение к процессу обработки металла.
1
Штамповка деталей из листового металла - под таким процессом понимают производство готовой продукции, разнообразных деталей и полуфабрикатов из металлов методом деформирования исходного сырья под давлением.
Подобную технологию знали еще наши далекие предки, которые посредством элементарного штампования изготавливали оружие, всевозможные украшения и предметы для домашнего обихода.
С 1850-х годов описываемый вид обработки начали модернизировать и технически совершенствовать, что позволило серийно производить штампованием разнообразные изделия массового спроса. Причем готовая штампованная продукция отличалась довольно-таки высоким качеством и превосходными эксплуатационными характеристиками.
С приходом 20 столетия листовая штамповка изделий из металла вышла на совершенно новый производственный и технический уровень. Благодаря ей начала развиваться сфера производства автомобилей (из штампованного материала делали кузова транспортных средств и многие другие детали). В 1930-х годах штампование взяли на вооружение судо- и авиастроительные предприятия, а через пару десятков лет она стала незаменимой для нужд ракетостроения.
Конструкции из штампованного металла характеризуются рядом особых свойств, что, в принципе, и обусловило популярность рассматриваемой технологии. К ее достоинствам относят следующие возможности:
- механизация и автоматизация производственных процессов, которые достигаются посредством внедрения мощных роторно-конвейерных линий оборудования;
- изготовление любых по геометрическим параметрам и формам готовых к применению изделий и разнообразных полуфабрикатов;
- производство высокоточных по размерам деталей, которые взаимозаменяют друг друга без необходимости их дополнительной обработке при помощи режущего инструмента и оборудования.
Кроме того, горячая и холодная штамповка гарантирует получение сравнительно "скромных" по массе металлических изделий с рациональными формами и высокими прочностными параметрами. Операции листовой штамповки позволяют производить как массивные заготовки для судо-, машино- и автостроительных предприятий, так и тонкостенные, буквально филигранные детали (например, тонкие стрелки для часов).
Нельзя не отметить отдельно также высокую производительность операции листовой штамповки и возможность получения при ее использовании совместно со сварочными мероприятиями любых по размерам узлов неразъемного типа, без коих не могут обойтись такие производственные отрасли, как судо- и вагоностроение.
2
Исходным сырьем для технологической операции выступают стальные полосы, тонкие ленты или листовой металл. По виду их обработки штамповка бывает двух видов: холодной; горячей. В большинстве случаев используется холодная штамповка. В тех случаях, когда мощность и производительность штамповочного оборудования является низкой, а также при небольшой пластичности заготовки рекомендована горячая штамповка. Обычно в горячем виде обрабатывают материал толщиной не более пяти миллиметров.
Технологический процесс штампования принято делить на такие операции: разделительные; формоизменяющие. Разделительные необходимы для разделения деформируемого участка изделия из металла по определенному контуру в процессе сдвига материала. К данным операциям относят:
- Резку: отделение по прямой либо кривой линии части заготовки (процесс выполняется последовательно). Резка производится гильотинными, дисковыми, вибрационными и другими видами ножниц при необходимости раскроя на полосы требуемых размеров металлических листов, а также при изготовлении готовых к эксплуатации изделий.
- Пробивку. Она используется тогда, когда в заготовке нужно получить разные по форме отверстия.
- Вырубку. Эта операция позволяет создать деталь, имеющую контур замкнутого вида.
А вот формоизменяющие операции осуществляются для модификации (без явления разрушения) геометрических размеров и конфигурации обрабатываемой детали. К ним причисляют:
- Отбортовку: создание вокруг отверстий и по контуру (наружному) изделия бортиков заданных размеров. Отбортовка, как правило, производится на концах трубных конструкций, к которым впоследствии планируется прикреплять фланцы.
- Вытяжку: получение пространственных полых изделий (полусферических, конических, цилиндрических, коробчатых и так далее) из исходных заготовок плоского вида.
- Обжим: сужение при помощи конической матрицы торцов полых и объемных деталей из металла.
- Гибку: придание изогнутой конфигурации плоским деталям.
- Формовку: наружный контур заготовки остается неизменным, а вот локальная ее форма изменяется по заданным параметрам.
Холодная штамповка подразумевает применение медных и алюминиевых сплавов (а также чисто медных и алюминиевых листов), легированной и . Нередко используются и материалы из группы неметаллов – пластмасса, кожа, плотный картон и другие.
Важным представляется то, что холодная обработка металла обеспечивает достаточно высокое качество поверхности полученных полуфабрикатов либо готовых деталей. Их чистота может в отдельных случаях достигать 8 класса. Хотя обычно таких требований к штампованному прокату потребители не предъявляют, их вполне устраивает чистота поверхностей на уровне 2–6 классов.
Заметим, что холодная штамповка листовых материалов увеличивает показатель удельной прочности готовых деталей, что отличает ее в лучшую сторону от стандартного металлического проката. Но при штамповании очень важно изучить и учесть все особенности материала, который используется для получения того или иного изделия. Для того чтобы холодная штамповка прошла качественно, необходимо принять во внимание следующие характеристики исходного сырья:
- магнитную и электрическую проводимость;
- твердость, механическую прочность;
- массу;
- ударную вязкость;
- теплостойкость и теплопроводность;
- долговечность, возможность противостоять коррозии и эксплуатационному износу.
3
Листовая штамповка производится в специальных штампах, сделанных из . Они в большинстве случаев имеют подвижную и неподвижную части, в которых монтируется пуансон и матрица (рабочие компоненты штампа). При сближении указанных частей происходит деформирование листового материала. Используя специальный пресс, выполняют крепление неподвижной и подвижной части. Вторая фиксируется в исполнительном устройстве, а первая – на столе, коим располагает пресс.
Как было сказано, штампы (а точнее их рабочие элементы) делают из дорогостоящих инструментальных сплавов. Но в тех случаях, когда выполняется штамповка мягких металлов (например, меди или алюминия), на материале штампа можно сэкономить, используя древесину, спрессованную в плотные валки, или пластмассу.
Также снизить расходы на штамповку крупных по размерам изделий, которые изготавливаются мелкими партиями, можно путем изготовления матрицы из бетона либо чугуна. При этом в качестве второй части штампа (пуансона) используют контейнер с водой. Его размещают над обрабатываемым изделием на матрице. Затем в воде путем подрыва заряда пороха (или воздействия электрическим разрядом) формируют требуемое давление, которое и деформирует лист металла по заданной матрицей форме.
Главное оборудование для штамповки – это . При помощи ножниц выполняют раскрой материала. Сейчас чаще всего используются вибрационные ножницы, характеризуемые легкостью эксплуатации и достаточной функциональностью. А вот пресс для штампования выбирают в зависимости от того, какие операции осуществляются. Как правило, используется кривошипный пресс, который бывает четырех-, двух- и однокривошипным. Работает он по достаточно простому принципу:
- двигатель, используя клиноременную передачу, передает через муфту на кривошипный вал необходимое движение;
- регулируемый по длине шатун передает движение далее (на ползун кривошипного устройства);
- на рабочий ход пресс запускается через муфту педалью.
Для обработки простых деталей применяются несложные по конструкции устройства. А вот для штамповки по-настоящему сложных изделий используют пресс особого типа, который снабжается несколькими ползунами.
Штамповка как технологический процесс обработки заготовок, изготовленных из металла, позволяет получить готовые изделия плоского или объемного типа, отличающиеся как своей формой, так и размерами. В качестве рабочего инструмента при выполнении штамповки может выступать штамп, закрепленный на прессе или оборудовании другого типа. В зависимости от условий выполнения штамповка металла бывает горячая и холодная. Эти два вида данной технологии предполагают использование различного оборудования и соблюдение определенных технологических норм.
Особенности технологии
Ознакомиться с требованиями ГОСТ к обработке металла штампованием можно, скачав документ в формате pdf по ссылке ниже.
Кроме разделения на горячую и холодную, штамповка изделий из металла подразделяется и на ряд других категорий в зависимости от ее назначения и технологических условий. Так, операции штамповки, в результате которых происходит отделение части металлической заготовки, называются разделительными. Сюда, в частности, относятся резка, рубка и пробивка деталей из металла.
Другой категорией таких операций, в результате которых штампуемый лист металла изменяет свою форму, являются формоизменяющие штамповочные операции, часто называемые формовкой. В результате их выполнения детали из металла могут подвергаться вытяжке, холодному выдавливанию, гибке и другим процедурам по обработке.
Как уже отмечалось выше, существуют такие виды штамповки, как холодная и горячая, которые, хотя и реализуются по одному принципу, предполагающему деформирование металла, имеют ряд значимых отличий. , предполагающую их предварительный нагрев до определенной температуры, применяют преимущественно на крупных производственных предприятиях.
Это связано прежде всего с достаточно высокой сложностью такой технологической операции, для качественного выполнения которой необходимо сделать предварительный расчет и точно соблюсти степень нагрева обрабатываемой заготовки. С помощью штамповки, выполняемой по горячей технологии, из листового металла различной толщины получают такие ответственные детали, как днища котлов и другие изделия в форме полусфер, корпусные и другие элементы, используемые в судостроении.
Для нагрева деталей из металла перед их горячей штамповкой используется нагревательное оборудование, которое в состоянии обеспечить точный температурный режим. В этой функции, в частности, могут использоваться электрические, плазменные и другие нагревательные устройства. Перед началом выполнения горячей штамповки необходимо не только рассчитать нормы нагрева обрабатываемых деталей, но и разработать точный и подробный чертеж готового изделия, в котором будет учтена усадка остывающего металла.
При выполнении металлических деталей процесс формирования готового изделия протекает только за счет давления, оказываемого рабочими элементами пресса на заготовку. За счет того, что заготовки при штамповке по холодной технологии предварительно не нагреваются, они не подвержены усадке. Это позволяет изготавливать изделия законченного вида, которые не требуют дальнейшей механической доработки. Именно поэтому данная технология считается не только более удобным, но и экономически выгодным вариантом обработки.
Если квалифицированно подойти к вопросам проектирования размеров и формы заготовок и к последующему раскрою материала, то можно значительно уменьшить его расход, что особенно актуально для предприятий, выпускающих свою продукцию крупными сериями. В качестве материала, заготовки из которого успешно подвергаются штамповке, может выступать не только углеродистые или легированные стали, но также алюминиевый и медный сплавы. Более того, оснащенный соответствующим образом штамповочный пресс успешно используется для обработки заготовок из таких материалов, как резина, кожа, картон, полимерные сплавы.
Разделительное штампование, целью которого является отделение от обрабатываемой заготовки части металла, – это очень распространенная технологическая операция, используемая практически на каждом производственном предприятии. К таким операциям, которые выполняются посредством специального инструмента, установленного на штамповочный пресс, относятся резка, вырубка и пробивка.
В процессе резки металлические детали разделяются на отдельные части, причем такое разделение может осуществляться по прямой или кривой линии реза. Для выполнения резки могут использоваться различные устройства: дисковые и вибрационные станки, гильотинные ножницы и др. Резку чаще всего используют для того, чтобы раскроить металлические заготовки для их дальнейшей обработки.
Вырубка – это технологическая операция, в процессе которой из металлического листа получают детали, имеющие замкнутый контур. При помощи пробивки в заготовках из листового металла делают отверстия различной конфигурации. Каждая из таких технологических операций должна быть тщательно спланирована и подготовлена, чтобы в результате ее выполнения получилось качественное готовое изделие. В частности, должны быть точно рассчитаны геометрические параметры используемого инструмента.
Перфорированный металлический лист получается в результате вырубки отверстий на координатно-пробивном прессе
Технологическими операциями штамповки, в процессе которых осуществляется изменение начальной конфигурации металлических деталей, являются формовка, гибка, вытяжка, отбортовка и обжим. Гибка – это наиболее распространенная формоизменяющая операция, в процессе которой на поверхности металлической заготовки формируются участки с изгибом.
Вытяжка – это объемная штамповка, целью выполнения которой является получение из плоской металлической детали объемного изделия. Именно при помощи вытяжки металлический лист превращается в изделия цилиндрической, конической, полусферической или коробчатой конфигурации.
По контуру изделий из листового металла, а также вокруг отверстий, которые в них выполнены, часто необходимо сформировать бортик. С этой задачей успешно справляется отбортовка. Такой обработке, выполняемой посредством специального инструмента, подвергают и концы труб, на которые необходимо установить фланцы.
При помощи обжима, в отличие от отбортовки, концы труб или края полостей в заготовках из листового металла не расширяют, а сужают. При выполнении такой операции, осуществляемой при помощи специальной конической матрицы, происходит наружное обжатие листового металла. Формовка, которая также является одной из разновидностей штамповки, предполагает изменение формы отдельных элементов штампованной детали, при этом наружный контур детали остается неизменным.
Объемная штамповка, которая может выполняться по различным технологиям, требует не только тщательных предварительных расчетов и разработки сложных чертежей, но и использования специально изготовленного оборудования, поэтому реализовать такую технологию в домашних условиях проблематично.
Инструменты и оборудование
Даже обработка мягких металлов, в частности штамповка алюминия, требует применения специального оборудования, в качестве которого могут выступать гильотинные ножницы, кривошипный или . Кроме того, необходимо умение производить расчеты расхода материала и разрабатывать технические чертежи. При этом следует учитывать требования, которые содержит соответствующий ГОСТ.
Штамповку, для выполнения которой не требуется предварительный нагрев обрабатываемой заготовки, выполняют преимущественно на гидравлических прессах, производство которых регулирует ГОСТ. Разнообразие серийных моделей этого оборудования позволяет подбирать станок для производства изделий различных конфигураций и габаритных размеров.
Выбирая пресс для выполнения штамповки, в первую очередь следует ориентироваться задачи, для решения которых он необходим. Например, для выполнения таких технологических операций, как вырубка или пробивка, используют штамповочное оборудование простого действия, ползун и шайбы которого в процессе обработки совершают небольшой ход. Для того чтобы выполнить вытяжку, требуется оборудование двойного действия, ползун и шайбы которого в процессе обработки совершают значительно больший ход.
По своей конструкции, как указывает ГОСТ, оборудование для выполнения штамповки делится на несколько типов, а именно:
- однокривошипное;
- двухкривошипное;
- четырехкривошипное.
На прессах двух последних категорий устанавливают ползуны более крупных размеров. Однако вне зависимости от конструктивного исполнения каждый штамповочный пресс оснащается матрицей. Основное движение, за счет которого и выполняется обработка заготовки на штамповочном прессе, совершает ползун, нижняя часть которого соединена с подвижной частью штампа. Для сообщения такого движения ползуну пресса приводной электродвигатель связывается с ним посредством таких элементов кинематической цепи, как:
- клиноременная передача;
- пусковая муфта;
- шайбы;
- кривошипный вал;
- шатун, при помощи которого можно регулировать величину рабочего хода ползуна.
Для запуска ползуна, который совершает возвратно-поступательное движение по направлению к рабочему столу пресса, используется ножная пресс-педаль, напрямую связанная с пусковой муфтой.
Несколько другим принципом работы отличается четырехшатунный пресс, рабочие органы которого создают усилие с центром, приходящимся на середину четырехугольника, образуемого четырьмя шатунами. Благодаря тому, что усилие, создаваемое таким прессом, приходится не на центр ползуна, это устройство успешно используется для того, чтобы изготавливать изделия даже очень сложной конфигурации. Прессы данной категории, в частности, применяют для того, чтобы изготовить асимметричные изделия, отличающиеся значительными габаритами.
Чтобы изготовить изделия более сложной конфигурации, используют прессовое оборудование пневматического типа, конструктивная особенность которого заключается в том, что оно может быть оснащено двумя или даже тремя ползунами. В прессе двойного действия применяются одновременно два ползуна, один из которых (внешний) обеспечивает фиксацию заготовки, а второй (внутренний) выполняет вытяжку поверхности обрабатываемого металлического листа. Первым в работе такого пресса, конструктивные параметры которого также регламентирует ГОСТ, участвует внешний ползун, фиксирующий заготовку при достижении самой нижней точки. После того как внутренний ползун выполнит свою работу по вытяжке листового металла, внешний рабочий орган поднимается и освобождает заготовку.
Для штамповки тонколистового металла используются преимущественно специальные фрикционные прессы, технические параметры которых также устанавливает ГОСТ. Чтобы обрабатывать более толстый листовой металл, лучше всего применять гидравлическое штамповочное оборудование, которое оснащено более надежными шайбами и другими конструктивными элементами.
Отдельную категорию составляет оборудование, при помощи которого выполняется штамповка взрывом. На таких устройствах, в которых энергия управляемого взрыва преобразуется в усилие, оказываемое на металл, обработке подвергают металлические заготовки значительной толщины. Работа такого оборудования, считающегося инновационным, даже на видео выглядит очень эффектно.
Штамповка металлических изделий осуществляется горячим и холодным методом при помощи пресса со штампом, формы и размеры которого по необходимости меняются. Возможно использование дополнительных рабочих составляющих. Разделительный тип изготовления предполагает следующие работы с металлом:
- пробивка;
- резка;
- рубка.
При холодном методе обработки допускается вытяжка металла, выдавливание, формовка и другие манипуляции.
Горячий метод штампования применяется для создания сферических объектов, а также в судостроении. Данная технология требует точного расчета, опыта, знания всех тонкостей получения металлоизделий путем высокотемпературной выпрессовки.
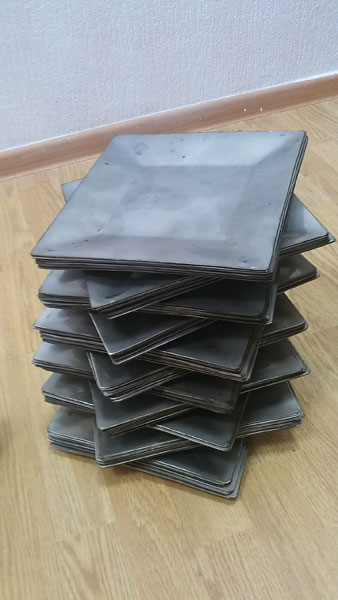
Сколько стоит штамповка
Штамповка изделий из нержавеющей стали пользуется большим спросом. Популярность изделий, полученных с применением данной технологии, вызвана несколькими факторами:
- умеренная стоимость;
- экономный расход сырья;
- высокая производительность.
Перечисленные преимущества особенно значимы для промышленного производства однотипных деталей.
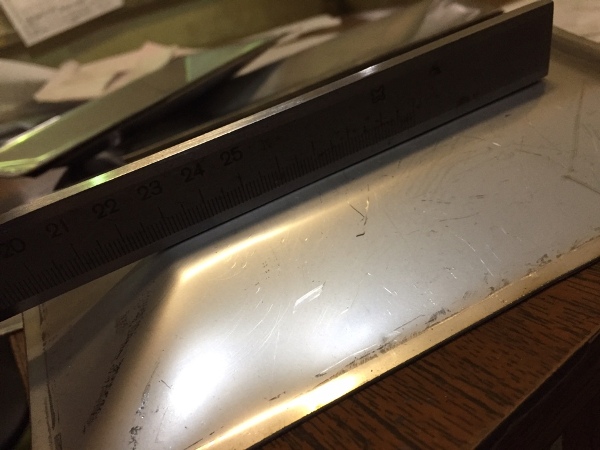
При пробивке, вырубке, резке металла нужно учесть пластические свойства материала, степень его растяжения, возможность утягивания и др. Процесс изготовления штамповки требует профессионального подхода, наличие специализированного инструментария, точного соблюдения технологии.
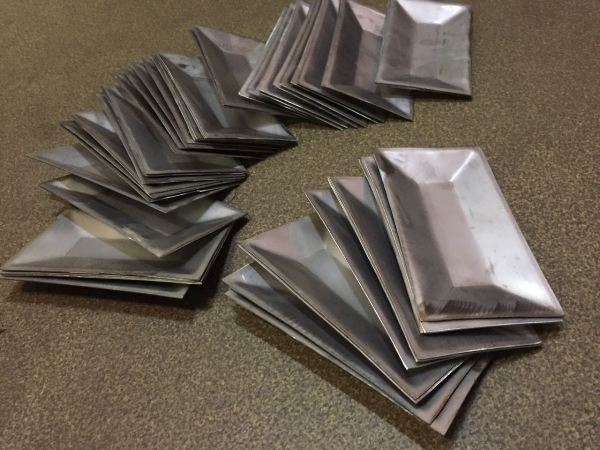
В цехах нашего холдинга работают настоящие специалисты, знающие все тонкости холодной и горячей штамповки. Мы гарантируем первоклассное выполнение операций разделительного и формоизменяющего штампования изделий.
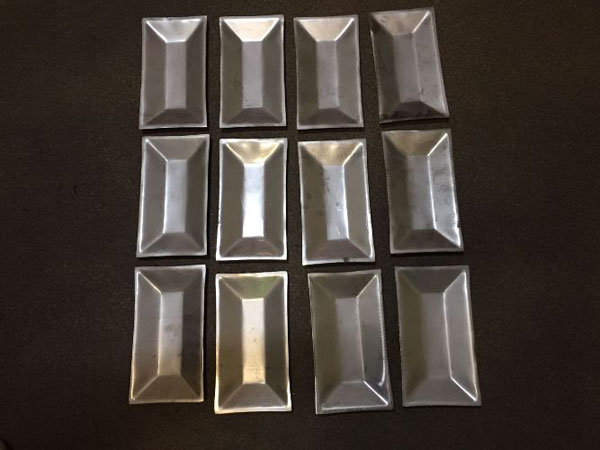
Разделительная штамповка (холодный метод)
Изготовление деталей идет с помощью вырезки, пробивки, вырубки. Резка металла проводится по кривым, прямым линиям, по запросу, с соблюдением требований. Вырубка применяется для создания заготовок с замкнутым контуром. Пробивка используется для получения различной конфигурации отверстий.
В компании «Металло Промышленный Холдинг» возможно изготовление форм из нержавеющей стали на заказ по выгодной стоимости. Мы осуществляем на заказ следующие виды обработки металлоизделий:
- формовку с сохранением наружного контура;
- гибку;
- обжим деталей выпуклого типа, содержащих внутреннюю полость. Манипуляция необходима для придания концевой части нужного сужения, производится при помощи матрицы конического вида;
- отбортовку для создания бортов снаружи изделия. Чаще применяется для обработки конечной части труб с фланцами;
- вытяжку, которая применяется для придания объема плоским заготовкам;
Преимущества сотрудничества с нашей компанией
«Металло Промышленный Холдинг» является одним из ведущих предприятий по изготовлению металлоизделий в нашем регионе. Материально-техническое оснащение наших производственных цехов позволяет выполнить штампование изделий высокой сложности в промышленных объемах. Привлекательные стороны сотрудничества:
- возможность реализовать заказ деталей в любом количестве;
- профессиональный подход;
- качество продукции;
- умеренная цена.
Развитие технологий в истории человечества дало дополнительные возможности и открыло перспективы. Вместе с тем, прогресс дает возможность применения имеющихся средств производства для изготовления новых товаров, рождая на них спрос.
Раньше из рук кузнецов редко выходили одинаковые вещи. Но с ростом населения и, соответственно потребностей, стали нужны не авторские работы, а массовое низкозатратное производство. В соответствии с необходимостью обработки металла с определенными свойствами, была осуществлена листовая штамповка металла. Кроме машиностроительных отраслей, производство деталей, один габарит которых во много раз меньше другого. Большинство плоских деталей, из метала или пластика, окружающих нас в жизни - изготовлены путем листовой штамповки.
Преимущества штамповки
Этот метод, основанный на применении прессах, позволяет достичь сразу нескольких целей. Во-первых, снизить стоимость производства одной детали - за счет применения высокотехнологичного оборудования, не требуется последующей обрезки детали.
Во-вторых, за одну рабочую смену на оборудовании возможен выпуск до нескольких тысяч одинаковых изделий. Это так же снижает себестоимость и уменьшает цену товара для потребителей. Производительность зависит, конечно же, от оборудования.
В-третьих, только листовая штамповка позволяет добиться минимальных отклонений габаритов от изначальной модели. Другие процессы массового производства имеют большую погрешность. К тому же часть производителей начинают разрабатывать свои конструкции с максимальным числом штампованных деталей.
Недорогие качественные изделия, производимые в большом количестве за малый срок - подобное сочетание предоставляет только листовая штамповка.
Проверка качества штампованной продукции осуществляется в ходе технологического цикла несколько раз: промежуточная проверка - после каждой технологической операции, и окончательная - после выхода готовой детали. Подобным достигается малый процент брака, и высокое качество.
Использование холодной штамповки металла в жизни весьма распространено, потому востребованность штамповки прослеживается не только в крупносерийных производствах, наподобие машиностроения, но и в среднем и мелком бизнесе. Так что - милости просим!