Технология штамповки деталей из листового металла. Штамповка листового металла: станки и прессы для холодной штамповки
Штамповка, для выполнения которой используется пресс для металла, является одной из наиболее распространенных технологических операций по обработке данного материала. Суть данной процедуры состоит в том, чтобы придать заготовке, изготовленной из металла, необходимую форму, для чего применяют пластическую деформацию, выдавливая определенный рельеф, узоры или осуществляя пробивку отверстий. Прессы для обработки металла в зависимости от перечня задач, для решения которых они предназначены, отличаются друг от друга как своими техническими параметрами, так и конструктивным исполнением.
Виды штамповочных технологических операций и оборудования
Штамповка как метод обработки заготовок из металла бывает:
- горячей;
- холодной.
Первая подразумевает, что металл подвергается обработке в нагретом состоянии. Большим преимуществом горячей штамповки является то, что при ее выполнении характеристики обрабатываемой заготовки улучшаются (в частности, структура металла становится плотнее и однороднее). Между тем на поверхности металлических заготовок, обрабатываемых по технологии , не создается слой окалины, при этом размеры готовых изделий получаются более точными, а их поверхность – более гладкой.
По типу заготовки, подвергаемой штамповке, такая технологическая операция может быть листовой или объемной. Штамповка первого вида применяется для обработки заготовок из листового металла, по такой технологии производят:
- посуду;
- ювелирные изделия;
- оружие;
- оборудование и инструменты медицинского назначения;
- детали часов, бытовой, климатической техники и электротехнического оборудования;
- детали для комплектации автомобильной техники;
- детали станков и другой машиностроительной продукции.
Готовые изделия из металла, полученные по технологии , не нуждаются в дальнейшей доработке. Формирование их геометрических параметров при выполнении объемной штамповки происходит в специальных формах, в которых горячий или холодный металл подвергается продавливанию.
Станок пресс обычно используется при:
- производстве заготовок из металла методом ковки;
- запрессовке и выпрессовке валов, подшипников и шестеренок;
- выполнении штамповки листового и объемного типа.
По принципу действия прессовальные станки могут относиться к механическому или гидравлическому типу, выполнять обработку металла статическими или ударными способами.
Прессовальное оборудование механического типа по своему конструктивному исполнению может быть:
- эксцентриковым;
- кривошипным.
Кривошипные станки используются как для холодной, так и для горячей . Применяется это штамповочное оборудование и для выполнения таких технологических операций, как вытяжка, вырубка и прорубка. Пресс гидравлический используется для штамповочных и кузнечных технологических операций с объемными металлическими заготовками.
По своим функциональным возможностям прессовальные станки подразделяются на следующие виды:
- универсальные;
- специальные;
- специализированные.
Универсальный прессовочный станок обладает самыми широкими функциональными возможностями, использовать такое оборудование можно для выполнения практически любой ковочной операции. Специализированные штампы или прессы применяются для реализации одного технологического процесса. Минимальной функциональностью обладают специальные прессы, которые используются для штампования изделий одного вида, при этом в основе их работы лежит одна технология.
Конструкция и принцип работы прессового оборудования
Конструкцию любого оборудования для штамповки составляют следующие элементы:
- приводной электродвигатель;
- механизм передачи движения;
- исполнительный механизм.
В зависимости от того, каким образом приводной двигатель пресса связан с его исполнительным механизмом, выделяют станки со связью:
- механической;
- немеханической, осуществляемой за счет жидкости, газа или пара.
В качестве исполнительного механизма, которым оснащается оборудование для выполнения штамповки, могут выступать траверсы, ползун, валки, ролики и бабы.
Прессы кривошипно-шатунного типа
Основным конструктивным элементом данных прессов является кривошипно-шатунный механизм, который преобразует вращательное движение, получаемое им от привода, в возвратно-поступательное движение ползуна. Исполнительный механизм, которым оснащается пресс штамповочный данного типа, связан непосредственно с ползуном, способным развивать усилие до 100 тонн. Движение ползуна в таких прессах осуществляется с одной и той же периодичностью.
Прессы кривошипно-шатунного типа могут относиться к оборудованию простого типа, двойного или тройного действия. Используя такие станки, можно выполнять следующие технологические операции:
- штамповку с использованием матриц открытого и закрытого типа;
- резку листового металла;
- прошивку;
- формирование готового изделия методом выдавливания;
- комбинированную обработку.
В тех случаях, когда для формовки готового изделия из металлической заготовки требуется более мощное оборудование, применяются станки гидравлического типа.
Гидравлические прессы
Используя гидравлический пресс, можно прессовать как более габаритные, так и более толстостенные детали из металла. Такое оборудование для листовой штамповки, объемной штамповки, ковки, гибки и других технологических операций в зависимости от конкретной модели может развивать усилия от 150 до 2000 тонн и даже более.
Основными конструктивными элементами, которыми оснащен любой , являются два цилиндра разного диаметра, которые наполнены рабочей жидкостью и сообщаются между собой. В каждом из таких гидравлических цилиндров установлен поршень, создающий давление рабочей жидкости или перемещающийся под его воздействием. Именно перемещением поршней в гидравлических цилиндрах обеспечивается движение исполнительного механизма оборудования. Величина усилия, которое может создавать такой штамповочный пресс, определяется разницей диаметров его гидроцилиндров.
Прессы радиально-ковочного типа
Радиально-ковочный станок – это формовочный пресс, на котором предварительно нагретые болванки из металла превращают в готовые изделия цилиндрической конфигурации. Конструкцию прессов данного типа составляют:
- индукционная печь, в которой происходит предварительный нагрев заготовки;
- конвейер для подачи заготовки в зону обработки;
- захватные механизмы, при помощи которых обрабатываемая деталь из металла, постоянно вращаясь, проходит через зону ковки;
- червячная передача, соединенная с электродвигателем и отвечающая за работу захватных механизмов;
- четыре вала с эксцентриковыми буксами, передающими движение шатуну с бойком, между которыми зафиксирован ползун (сами валы посредством клиноременной передачи получают вращение от приводного электродвигателя);
- копирные барабаны, отвечающие за синхронное сближение бойков и последующее движение заготовки;
- пружинная муфта, обеспечивающая торможение детали в момент ее обработки бойками.
Прессы электромагнитного типа
Это новый вид прессовального оборудования. Принцип его действия основан на свойствах сердечника, помещенного в проволочную катушку, через которую проходит электрический ток, и совершающего перемещения под воздействием электромагнитного поля. Сердечник электромагнита таких прессов воздействует на исполнительный механизм станка, направляя его к обрабатываемой заготовке из металла.
Отличительными характеристиками электромагнитных прессов являются высокая производительность выполняемой обработки и экономичность использования.
При разработке технологического процесса штамповки выполняют технологические расчеты, которые включают определение необходимого усилия вырубки и пробивки, усилие пресса, формы и размеров заготовки, необходимого количества операций и их последовательности.
Усилие вырубки и пробивки, необходимое для штампа, у которого соответствующие режущие грани пуансона и матрицы параллельны между собой, зависит от периметра вырубки р, толщины штампуемого материала s, сопротивления срезуматериала заготовки, формы и состояния рабочих кромокпуансона и матрицы и зазора между ними, скорости деформирования и глубины внедрения пуансона в металл в момент появления скалывающих трещин.
При расчетах усилие вырубки и пробивки Р (МПа) приближенно определяют как произведение площади боковой поверхности F,отделяемой части металла, на сопротивление срезу :
Р=К F = К рs
Где К–коэффициент. Учитывающий влияние затупления режущих кромок штампа, нервномерности материала заготовки и других факторов, влияющих на повышение усилия вырубки в процессе штамповки.Рекомендкемые значения к=1.3–1,6.
Сопротивление материала срезу,Па:
Где –разрушающее напряжение при разрыве, принимается по наибольшему предельному значению, предусмотреннему ГОСТ для соответствующей марки стали, Па. Так, например, требования к механическим свойствам сталей 2011,2013 по ГОСТ 21427 =300….500 Мпа.
Требуемое усилие штамповки, Н
где Р–усилие сжатия буферного устройства для съёмников, Н:
Величина силы сжатия в штампе принимается в зависимости от усилия,небходимого для снятия полосы с пуансона, которое в свою очередь зависит от толщины пробиваемого материала и схемы штамповки.Чем толще материл, тем больше усилие.Значение величин усилий при штамповке необходимо для расчёта деталей штампа на прочность и выбора пресса с усилием, обеспечивающим штамповку данной детали.
Выбор пресса осуществляется по требуемому усилию штамповки исходя из условия:
Усилие пресса,указанное в его паспорте, должно быть равно или больше расчётного, в пртивном случае поломка пресса неизбежна.
3.8 Оборудование,применяемое для штамповки листов сердечников
Для изготовления листов сердечников в цехах холодной штамповки применяют ножницы листовые с наклонными ножами и многодисковые,а также штамповочные прессы.
Перед штамповкой листовой прокат,поступающий со склада,как правило,приходится разрезать на полосы требуемой ширины для различных штампов.Для этого применяют ножницы листовые с наклонными ножами(гильотинные ножницы) или многодисковые (роликовые).
Ножницы листовые с наклонными ножами (рис. 3.9, а) позволяют выполнять прямолинейную резку листов на полосы или отдельные заготовки из металла толщиной от 0,3 до 16 мм и шириной до 3 м. На ножевой балке (1) закреплен верхний подвижный нож (2), а на ножевой балке (4) закреплен нижний неподвижный нож (3). Угол наклона верхнего ножа выбираютв зависимости от толщины разрезаемого листа от 1° 10" до 3° 15". Разрезаемый лист укладывают на стол ножниц и подают до упора. При включении ножниц перед разрезкой лист предварительно прижимается к столу прижимом, а затем разрезается ножами.
Рисунок 3.9 - Ножницы листовые:
а - с наклонными ножами, 6 - дисковые ножницы; 1 - верхняя ножевая балка, 2 - верхний подвижный нож, 3 - нижний неподвижный нож, 4 - нижняя ножевая балка, 5 - параллельные валы, 6 - пара дисковых ножей
Многодисковые ножницы (рис. 3.9, 6) имеют два параллельных вала (5), на которых закреплены несколько пар дисковых ножей (6), разрезающих лист на полосы. Дисковые ножи могут передвигаться на валах. Каждую пару ножей устанавливают и закрепляют друг от друга на расстояние, равное ширине полосы. Многодисковыми роликовыми ножницами разрезают, как правило, листы из электротехнической стали на полосы для штамповки железа сердечников. Такие ножницы позволяют резать листы на полосы из металла толщиной от 0,3 до 3 мм и шириной 300...800 мм. Роликовые ножницы более производительны,чем ножницы с наклонными ножами., так как на них лист раскраивается сразу на несколько полос.
Штамповочные прессы для холодной штамповки по технологическому признаку подразделяют на:
универсальные, на которых можно выполнять различные штамповочные операции (вырубные, пробивные, гибочные);
специальные, которые предназначены для выполнения лишь отдельных операций или изготовления отдельных деталей.
Универсальные прессы бывают механические (кривошипные) и гидравлические. Для изготовления листов сердечников электрических машин методом холодной штамповки применяют, как правило, механические кривошипные прессы. В таких прессах движение рабочим органам передается от элек-тродвигателя при помощи механической передачи. Для преобразования вращательного движения двигателя в возвратно-поступательное движение ползуна используют кривошипно-шатунный (эксцентриковый) механизм. В этих прессах используется кинетическая энергия вращающегося маховика. Схема устройства кривошипного пресса показана на рис.3.10, а. Принцип работы кривошипного пресса заключается в следующем: от электродвигателя (8) через зубчатую передачу вращение передается маховому колесу (маховику) (7), которое свободно сидит на конце кривошипного вала (5). От маховика кривошипному валу вращение передается через муфту (6), одна половина которой жестко соединена с маховиком, а другая - с кривошипным валом. Муфта включается через систему передач при нажатии на педаль (1). При этом вал, вращаясь, делает вокруг своей оси один оборот, а ползун (3) с шатуном (4) - один двойной ход.
При вращении кривошипа (9) (рис. 3.10 б) по окружности ползуну (3) через шатун (4) сообщается возвратно-поступательное движение. Ползун пресса имеет два конечных положения, одно из которых называется верхней мертвой точкой (ВМТ), второе - нижней мертвой точкой (НМТ). Расстояние от ползуна в его ВМТ до стола пресса (рис.3.10 а ) называют открытой высотой, а расстояние от ползуна в его НМТ до стола - закрытой высотой пресса. Величину хода пресса определяют расстоянием между верхней и нижней мертвыми точками. Усилие на ползуне переменное и зависит от положения кривошипа. Наибольшим оно будет в ВМТ и НМТ. В паспорте пресса указывают его номинальное усилие, когда кривошип не доходит до НМТ примерно на 20.. .30° (угол ).
Рисунок 3.10 - Кривошипный пресс:
а - схема устройства пресса, 6 - схема работы кривошипно-шатунного механизма, в - схема установки штампа на стол пресса; 1 - педаль включения, 2 - стол пресса, 3 - ползун, 4 - шатун, 5 - кривошипный вал, 6 - муфта, 7 - маховое колесо, 8 - электродвигатель, 9 - кривошип
При работе пресса с одиночными ударами после каждого хода пресс автоматически включается. Управление прессом предусматривает его работу на самоходе. Это необходимо при штамповке деталей с автоматической подачей заготовок в штамп. Нижнюю часть штампа крепят на столе пресса (2), а верхнюю - на ползуне (3), который движется в направляющих. Существует много разновидностей кривошипных прессов, которые отличаются друг от друга усилием, конструкций станины и муфты включения, формой кривошипного вала и др. Для вырубки листов сердечников электрических машин применяют кривошипные прессы с небольшим ходом ползуна. При проектировании штампов необходимо их размеры согласовать с соответствующими размерами пресса.
Штамп на стол пресса можно устанавливать лишь в том случае, если закрытая высота штампа Н(рис.3.10 в) будет на 5...6 мм меньше закрытой высоты пресса Н, в противном случае при ходе ползуна вниз может произойти поломка пресса или штампа. Закрытая высота пресса может регулироваться в определенных пределах за счет изменения длины шатуна, имеющего винтовое соединение с ползуном. Благодаря этому на пресс можно устанавливать штампы с различной закрытой высотой
Специальные пресс-автоматы применяют в массовом производстве для штамповки листов сердечников статоров и роторов электрических машин. Пресс-автоматы с нижним приводом предназначены для двухрядной штам-иовки многопозиционными штампами последовательного действия листов сердечников электродвигателей с высотой оси вращения 56 и 63 мм. Такие пресс-автоматы обладают высокой производительностью и доступным расположением штампов, а за счет регулировки втулок направляющих колонок инструменту сообщается точное направление.
Пресс-автоматы с нижним приводом выпускаются с числом ударов в минуту от 80 до 280.
Прессы типа «Бакинец», разработанные Бакинским отделением ВНИИТэлектромаш, предназначены для штамповки из полосы или рулона шириной до 500 мм листов статора и ротора с использованием совмещенных штампов. Пресс двухэтажный имеет два ползуна 1 и 2, расположенных один над другим и перемещающихся на четырех колонках по направляющим втулкам станины. От центрального вала 3, на который установлена пневматическая муфта, одновременно являющаяся и маховиком, вращаются два коленчатых вала, которые сообщают возвратно-поступательное движение обоим ползунам пресса. Штамповка производится двумя совмещенными компаундными штампами 4 и 5, расположенными один над другим.
Рассмотрим технологическую схему штамповки (рис. 3.11); Материал подается в верхний штамп 1 и производится вырубка статорного листа 10 и заготовки ротора 9, Статорный лист сбрасывается с пуансона в момент полного открытия штампа, равного 80 мм, попадает на лоток 2 и по нему транспортируется на ста-пелирующую оправку 7. Заготовка ротора под собственным весом падает в ловитель 3. Работа ловителя 3 согласована с работой нижнего штампа 4 для штамповки роторного листа 8. Из ловителя 3 заготовка падает на ловитель штампа 4, в котором производит-
ся вырубка листа ротора. Готовый лист ротора по лотку 5 посту: пает на стапелирующую оправку 6. Работа верхнего штампа, ловителя и нижнего штампа синхронизирована.
Рисунок 3.11–Технологическая схема штамповки на прессе-автомате типа” Бакинец”
При штамповке из рулона пресс снабжается разматывающим устройством, а при штамповке из полосы подача осуществляется блоком вакуумных присосов. Присосы, работая синхронно с ходом ползунов, берут верхнюю полосу из стопы и, поворачивая ее на 90°,передвигают в зону штампа с помощью валковой подачи.Точность подачи не играет большого значения, так как листы статора и ротора штампуются за один удар штампа. На прессе можно штамповать полосы горячекатаной электротехнической стали с пониженными требованиями: без предварительной калибровки по длине, с непараллельностью кромок полос до 3 мм и саблевидностью полосы до 3 мм, без ограничения норм волнистости и коробковатости полос. Распушение полос при взятии их из кассеты исключает слипание и подачу сдвоенных полос под штамп. Пресс обслуживает один оператор. Стойкость штампов при работе на прессе «Бакинец» значительно выше стойкости штампов при работе на универсальных прессах, что обусловлено рядом конструктивных особенностей. В конструкции штампов применены жесткие стальные блоки плит и шариковые направляющие колонок. Штампы и полосы продуваются и смазываются, а вертикальное расположение штампа исключает засорение режущих частей. Прессы типа «Бакинец» изготавливаются усилием до 4 МН. Производительность пресса достигает 20-25 тыс. комплектов листов в смену.
Последовательная штамповка по системе “Тандем” многопозиционными штампами является весьма прогрессивной, но для штамповки листов статора и ротора больших диаметров (свыше 250-350 мм) не применяется вследствие увеличения габаритов многопозиционных штампов (особенно при значительных диаметрах листов магнитопроводов), что усложняет и повышает стоимость их изготовления и эксплуатацию, и соответственно увеличения габаритов пресса (а следовательно, и удорожания).
В последние годы применяется последовательная штамповка, листов магнитопроводов по системе «Тандем», сущность которой состоит в том, что штамповка производится на двух последовательно работающих прессах с двумя штампами. С помощью сельсинного устройства оба пресса работают синхронно с минимальной разницей скоростей в пределах одного хода, что позволяет устанавливать минимальную компенсационную петлю между прессами. Установка (рис. 3.12) работает следующим образом.С размотчика 1 через правильное устройство 2 лента попадает в подающее устройство 3. Между правильным и подающим устройством имеется первая компенсационная петля материала 10 На первом прессе 4 в двухпозиционном штампе вырубается лист ротора 9. На первой позиции вырубаются пазы ротора, вентиляционные отверстия и отверстия под вал. На второй позиции обсекается наружный диаметр листа ротора, и он удаляется из зоны штамповки либо на провал, либо в боковое окно пресса. Между прессами материал имеет вторую компенсационную петлю 8. Устройство 5 подает ленту, и второй пресс 6 за два или три удара вырубает лист статора 7. Производится пробивка пазов и обсечка наружного контура. Лист удаляется на провал либо в боковое окно. Фиксация рулона происходит ловителями штампа на четыре технологических отверстия. Отходы материала после выхода из; второго ^пресса измельчаются для удобства транспортировки и пакетирования.
Рисунок 3.12–Расположение прессов и схема штамповки по системе “Тандем”
Система «Тандем» позволяет обеспечить автоматическую последовательную штамповку листов магнитопровода диаметром до 600 мм. При этом длина штампов уменьшается в 2 раза, упрощается их изготовление и эксплуатация, повышается стойкость штампов, так как затачивается каждый штамп отдельно, в то время как в многопозиционном штампе затачивается вся рабочая поверхность. Отпадает необходимость в прессах большой мощности (4 МН и более), обеспечивается равномерная загрузка прессов.
Все операции холодной штамповки выполняются на прессах. В зависимости от условий обработки и характера изготовляемых деталей применяются различные типы прессов.
По виду привода различают прессы механические, гидравлические, пневматические, электромагнитные и ручные. В холодноштамповочном производстве применяются обычно прессы с механическим и гидравлическим приводом; пневматические, электромагнитные и ручные прессы используются преимущественно при выполнении запрессовочно-сборочных операций.
По способу воздействия на штампуемый материал как механические, так и гидравлические прессы разделяются на прессы простого, двойного и тройного действия.
Прессы простого действия имеют один движущийся ползун и применяются для самых разнообразных штамповочных работ -вырубки, пробивки, гибки, неглубокой вытяжки, формовки и др.
Прессы двойного действия имеют два независимо движущихся ползуна, размещенных один внутри другого. Наружный ползун является прижимным, а внутренний- вытяжным. Прессы двойного действия применяются в основном для вытяжки листового материала, но на них часто выполняют формоизменяющие и разделительные операции..
Прессы тройного действия имеют два верхних и один нижний ползун, выполняющий вытяжку в обратном направлении, или два ползуна и движущийся навстречу стол. Эти типы прессов применяются для выполнения сложной глубокой вытяжки листовых деталей. На рис. 48, а и б показаны схемы штамповки на прессах простого и двойного действия.
Из прессов простого действия наиболее распространены кривошипные и эксцентриковые. Они бывают открытого и закрытого типа.
Кривошипные и эксцентриковые прессы подразделяются по типу станин на одностоечные (открытые) и двухстоечные. Одностоечные прессы имеют кривошипно-шатунный механизм, расположенный на консольном конце рабочего вала, а на двухстоечных - шатун расположен в середине опор коленчатого вала.
Рис. 48. Схемы штамповки на прессах : а - на прессе простого действия, б - на прессе двойного действия (Р - усилие верхнего прессования, Q - усилие прижима)
Вращательное движение вала преобразуется в возвратно-поступательное движение ползуна кривошипно-шатунным механизмом. Кривошип, вращаясь, определяет два положения ползуна: крайнее нижнее и крайнее верхнее. Расстояние между верхним и нижним крайними положениями называется ходом ползуна. За один оборот кривошипа ползун делает два хода: вниз и вверх. Штамповка осуществляется только при ходе ползуна вниз.
В кривошипных одностоечных прессах открытого типа усилием до 100 Т ход ползуна может быть постоянным и регулируемым.
К преимуществам эксцентриковых прессов относится возможность простого регулирования величины хода ползуна поворотом втулки верхней головки шатуна на эксцентрике вала. В кривошипных прессах такая возможность встречается редко, так как в большинстве конструкций верхняя головка шатуна соединена непосредственно с шейкой вала.
Для прижима заготовки при вытяжке или гибке и для выталкивания деталей из нижней части штампа применяются буферные устройства, которые обычно прикрепляют к нижней части пресса под столом. По конструкции и принципу действия буферные устройства бывают пружинные, резиновые, пневматические, а также пнев-могидравлические и гидравлические.
Прессы мощностью до 100 Т обычно оборудуют пружинными или резиновыми буферными устройствами. Эти устройства просты по конструкции, но имеют недостаток, заключающийся в том, что по мере сжатия их сопротивление возрастает, и поэтому в конце хода усилие прижима или выталкивания значительно больше, чем в начале операции.
Пневматические, пневмогидравлические и гидравлические буферные устройства дают возможность получать постоянные усилия прижима или выталкивания в процессе рабочей операции и, кроме того, часто используются для приведения в действие различных узлов штампов.
Все эксцентриковые и кривошипные прессы имеют устройства, предохраняющие кривошипно-шатунный механизм от поломок при перегрузке. Обычно перегрузка пресса прежде всего отражается на шатуне. Поэтому в зависимости от конструкции шатуна под подпятник шаровой головки или под торец цилиндрического утолщения на опорное кольцо кладут предохранительную шайбу, которая при перегрузке пресса срезается и может быть быстро заменена.
Гидравлические прессы подразделяются в основном на прессы простого, двойного и тройного действия. Они бывают с приводом от централизованного аккумулятора, питаемого насосом, или с индивидуальным приводом от одного или нескольких насосов.
У прессов двойного действия наружный рабочий ползун и перемещающийся внутри него вытяжной ползун могут двигаться как вместе, так и отдельно. Штамповка на них, во избежание образования складок, выполняется с прижимом края листовой заготовки.
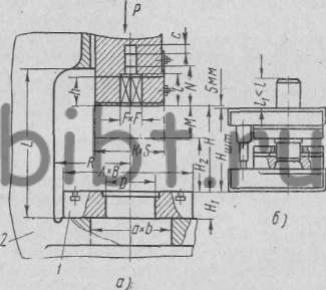
Рис. 49, Параметры характеристики пресса (а) и соответствующие им параметры штампа (б): 1 -подкладная плита, 2- стол пресса
Листоштамповочные гидравлические прессы по сравнению с прессами других типов имеют значительно большее межштамповое пространство, необходимое для прессования деталей из заготовок большого размера. Усилие прессов очень высокое - от 150 до 2000 Т и более.
Технические характеристики прессов. Основными характеристиками пресса являются следующие (рис. 49, а).
Номинальное усилие пресса Р в тоннах- наибольшее усилие, которое без нарушения прочности основных узлов пресса может быть приложено к ползуну при повороте кривошипа, от нижнего нулевого положения на угол не более 30°.
Для кривошипных прессов двойного действия номинальное усилие внутреннего ползуна определяет наибольшее усилие вытяжки, а номинальное усилие наружного ползуна - наибольшее усилие прижима. В прессах двойного действия, выпускаемых в СССР, это соотношение принято для однокривошипных прессов 1,4:1,6. для двухкривошипных 1:1.
Длина хода ползуна h в миллиметрах - расстояние между верхним и нижним положением ползуна, т. е. путь, который проходит ползун за время половины оборота вала. Длина хода в некоторых прессах может изменяться за счет поворота эксцентриковой втулки. В этом случае наибольший ход ползуна равен удвоенной сумме эксцентриситетов втулки и вала, а наименьший - их удовоенной разности. Если втулка установлена так, что ее наибольший эксцентриситет совпадает с наибольшим эксцентриситетом вала, то получается наибольший ход.
В паспорте пресса обычно указываются наибольший, наименьший и промежуточный ходы, которые можно получить на данном прессе. Величина хода определяет возможность применения пресса для различных операций.
Число двойных ходов ползуна в минуту п необходимо знать для расчета скорости движения ползуна и производительности пресса. В паспортах указывается число двойных ходов в минуту при включении на непрерывную работу.
Величина регулирования длины шатуна М в миллиметрах (разность между наибольшей и наименыней длиной шатуна) определяет изменение пределов закрытой высоты пресса. Наибольшая закрытая высота пресса Н миллиметрах - расстояние от плиты до ползуна в его нижнем положении при максимальном ходе и наименьшей длине шатуна. Определяется при любом ходе прибавлением к закрытой высоте, указанной в паспорте, полуразности наибольшего хода, и хода, при котором определяется закрытая высота.
Наименьшая закрытая высота пресса H2 определяется как разность между H и M.
Расстояние от стола пресса до направляющих обозначается буквой L.
Вылет ползуна R в миллиметрах -расстояние от оси ползуна до станины - определяет собой наибольшее расстояние от оси хвостовика до заднего выступа штампа, устанавливаемого на прессе.
Размеры ползуна К X S и стола (или подштамповой плиты) А X В в миллиметрах указываются справа налево и спереди назад и служат для определения габаритных размеров штампов, которые могут устанавливаться на данном прессе.
Размеры отверстия в столе а x b и подштамповой плите D обусловливают возможность выпадения вырубленной детали или отхода и установки буферного устройства.
Размеры квадратного отверстия в ползуне F*F*l (сечение X глубина) определяют размеры хвостовика для крепления верхней части штампа.
Размер С определяет наибольший ход верхнего выталкивателя, что указывает на глубину возможной вытяжки стакана при условии, если стакан вытягивается дном вверх.
Размер N показывает расстояние от выталкивателя до нижней поверхности ползуна.
Толщина подштамповой плиты H1 в миллиметрах, которую следует вычитать из закрытой высоты штампа, взятой по паспорту, определяет возможную закрытую высоту штампа, устанавливаемого на подштамповую плиту пресса.
Высота штампа Hшт (рис. 49,б) определяется, как правило, в его нижнем рабочем положении, так как в этом положении наилучшим образом согласовывается взаимодействие верхней и нижней рабочих частей штампа, его прижимающих и удаляющих деталей. Высота штампа не должна превышать закрытую высоту пресса.
Практически закрытая высота штампа (в нижнем рабочем положении) должна находиться между наибольшей закрытой высотой пресса Н и наименьшей закрытой высотой пресса Н2. На рис. 49 показан условно минимальный зазор между Н и H шт, равный 5 мм. Если закрытая высота штампа Hшт будет значительно меньше H2 пресса, необходимо применять промежуточные подкладные плиты или подкладывать под нижнюю плиту штампа специально обработанные бруски.
Пресс штамповочный, при помощи которого выполняется ковка металлических заготовок, работает по достаточно простой схеме. Принцип его работы, по сути, схож с принципом действия обычного молотка, которым наносятся удары по металлическому изделию, чтобы деформировать его и придать ему требуемую конфигурацию.
Штамповочные прессы гидравлического и кривошипного типа
С того момента, как люди научились выполнять обработку металла давлением, работа специалиста, который ей занимался, считалась одной из самых почетных. С течением времени потребность в металлических изделиях, полученных по технологии ковки, только возрастала, в них стала нуждаться и активно развивающаяся промышленность. Все это привело к тому, что для ковки стал использоваться не ручной труд кузнецов, а специальное оборудование для штамповки.
Достаточно распространенным типом устройств, используемых для ковки, является своеобразный аналог молота – штамповочный пресс. Применяя такое штамповочное оборудование, можно выполнять целый перечень технологических операций, а именно: изменение формы заготовки путем ее пластической деформации, формирование на ее поверхности заданного рельефа, вырубание отдельных фрагментов и др. На таком устройстве, в частности, придают форму заготовкам, для изготовления которых было использовано литье. Прессы, применяемые для штамповочных операций, могут быть кривошипными или гидравлическими.
Пресс кривошипный применяют в тех случаях, когда необходимо выполнить несложную обработку металла давлением. Основным элементом такого оборудования, который преобразует вращательное движение вала приводного электродвигателя в возвратно-поступательное перемещение ползуна, является кривошипно-шатунный механизм. Именно поэтому пресс кривошипный часто называют штамповочным кривошипно-шатунным прессом. Он очень популярен как среди производственников, так и среди частных мастеров, существуют даже модели настольного кривошипного пресса. Объясняется такая популярность не только высокой эффективностью и функциональностью этого оборудования, но также и тем, что обслуживание и ремонт кривошипных прессов не вызывает особых проблем.
Оснащаются двумя рабочими камерами, в которых в рабочей жидкости создается требуемое давление. Жидкость под давлением поступает в цилиндр с другим поршнем, посредством которого и сообщается возвратно-поступательное движение ползуну.
Радиально-ковочное оборудование для горячей обработки металла
Радиально-ковочный станок используется для того, чтобы с высокой производительностью изготавливать валы различного диаметра. На таком агрегате можно наладить производство до 300 тысяч готовых изделий в год, чего вполне достаточно для того, чтобы обеспечить ими крупное производственное предприятие.
Ограниченность использования такого станка для штамповки металла объясняется не только его высокой стоимостью, но еще и тем, что настройка его рабочих режимов представляет собой достаточно сложный процесс, поэтому выполнять ее целесообразно лишь в том случае, если планируется выпускать изделия определенного диаметра большими партиями.
Последовательность действий, в процессе которых выполняется радиальная ковка, выглядит следующим образом.
- Деталь, чтобы довести ее до требуемой температуры нагрева, подают в индукционное устройство.
- После того как металл приобретет требуемую степень пластичности, деталь по роликовому контейнеру (рольтангу) отправляют к захватному устройству, с помощью которого она подается в зону обработки.
- Там заготовка фиксируется элементами другого захватного устройства, после чего на нее воздействуют посредством специальных бойков.
- Для равномерной обработки со всех сторон деталь постоянно вращают, для чего используется специальный захватный механизм.
Для того чтобы привести в движение рабочий механизм оборудования для радиальной ковки, используют кинематическую схему, элементами которой являются:
- приводной электродвигатель;
- клиноременная передача;
- четыре установленных вертикально вала с эксцентриковыми буксами;
- шатун с закрепленными на нем бойком и ползуном.
Основные элементы автоматики станка – это копирные барабаны, которые отвечают как за синхронное сближение бойков, так и за последующее движение заготовки. Вращение захвату, в котором удерживается обрабатываемая деталь, сообщается электродвигателем через элементы червячной передачи. Торможение данного механизма, которое осуществляется в момент ковки, обеспечивает пружинная муфта.
Одной из разновидностей ковочного оборудования является горизонтально-ковочный станок, в котором обрабатываемая деталь также располагается параллельно земле. Устройства данного типа используются преимущественно для формирования торцевых утолщений на заготовках стержневого типа. Деталь при обработке располагается в разъемной матрице, каналы которой ориентированы в горизонтальной плоскости.
Процесс обработки, выполняемой на таком станке, происходит в следующей последовательности.
- Заготовка укладывается в неподвижную часть матрицы.
- Подвижная часть матрицы, соединенная с ползуном, приводится в действие посредством коленчатого вала.
- Приближаясь к неподвижной половине формы, подвижная часть матрицы плотно охватывает обрабатываемый стержень.
- После зажима детали верхней частью формы коленчатый вал, соединенный с шатуном, приводит в действие ударные пуансоны.
- По окончании обработки все подвижные части станка возвращаются в исходное положение, а подвижная и неподвижная части формы размыкаются.
Ковочный молот с пневмоприводом
Пневматический пресс – это эффективное, но в то же время доступное по стоимости ковочное оборудование, отличающееся, кроме того, компактными габаритами. Работает такой станок за счет энергии сжатого воздуха, за подачу которого к механизмам отвечает встроенный компрессор. Работу компрессора, поршни которого, двигаясь в его главном цилиндре, как раз и создают поток воздуха с требуемым давлением, обеспечивает приводной электродвигатель.
Поскольку работу ударного механизма пневматического ковочного станка обеспечивает кривошип, то его конструкция напоминает устройство кривошипного пресса. Перед запуском такого оборудования компрессорный и рабочий поршни в главном цилиндре находятся в крайнем верхнем и крайнем нижнем положениях. Когда станок запускается в действие, поршни начинают двигаться по направлению друг к другу, сжимая находящийся между ними воздух, давление которого передается на кривошип, напрямую соединенный с бойком. На один удар рабочей части молота пневматического станка приходится один оборот кривошипного механизма. Соответственно, чтобы воздействие молота на заготовку выполнялось с более высокой частотой, необходимо обеспечить более интенсивную работу компрессора. Даже несмотря на свои небольшие габариты, пневматический пресс может обеспечить массу удара молота, доходящую до 1 тонны.
По похожему с пневматическим прессом принципу работает паровоздушный молот, в котором энергию удара обеспечивает горячий пар, подающийся непосредственно из котла или через специальный компрессор. Масса ударов, которой позволяет добиться такое оборудование, может доходить до 8 тонн, а скорость их нанесения составляет 50 м/сек. Работать оно в зависимости от модели может в автоматическом режиме, когда удары по детали наносятся непрерывно, или в ручном, когда для запуска в действие бойка необходимо нажать на соответствующую кнопку или педаль.
Механические молоты могут использоваться для:
- свободной ковки или ковочных операций, при выполнении которых для формирования готового изделия используется прессформа;
- штамповочных операций с деталями из листового металла – резки по ровной или кривой линии, вырубки по различному контуру, пробивки отверстий (дыропробивной пресс) и др.;
- выколотки – изготовления изделий с использованием специального шаблона.
Ковочное оборудование ротационного и вальцевого типа
На крупных производственных предприятиях для выполнения ковочных операций часто применяется конвейерное оборудование вальцевого типа. Заготовки на нем обрабатываются методом обжима, который выполняют вращающиеся вальцы. По похожему принципу работают и ротационно-ковочные машины, обработка деталей в которых также осуществляется в процессе вращения рабочих органов.
Штамповка — это один из наиболее частых видов обработки металла, который представляет собой деформацию, придающую детали необходимую форму методом выдавливания на поверхности определенного рельефа, узора, отверстий. Процесс этот осуществляется на специальных прессах различной конструкции.
Виды штамповки и оборудования
На производстве используются два вида штамповки:
- горячая;
- холодная.
При горячем способе обрабатывается нагретый металл. При этом улучшаются качества материала: он становится плотнее, однороднее. Плюс холодного метода в том, что на поверхности не появляется слой окалины, размеры детали получаются точнее, поверхность глаже.
Штамповка может быть листовой или объемной. Листовым методом производят: посуду, ювелирные изделия, детали часов, климатической техники и микросхем, оружие, медицинское оборудование, детали для автомобиле-, машино- и станкостроения. Полученные детали не требуют дальнейшей обработки. В ходе объемного прессования холодный или раскаленный металл продавливается в формах.
В металлообработке прессы используются для:
- производства поковок;
- запрессовки шестеренок, подшипников;
- объемной и листовой штамповки.
Станки для прессования могут основываться на принципах механики или гидравлики, обрабатывать материалы статическим или ударным способом.
Механические бывают:
- эксцентриковые;
- кривошипными.
Кривошипные станки выполняют холодную и горячую штамповку металла давлением: вытяжку, вырубку и прорубку. Гидравлические прессы используются для объемной кузнечной обработки металла. Согласно технологическим возможностям прессы делятся на: универсальные, специальные и специализированные. Универсальные можно использовать практически для любых видов ковки (пример — гидравлический ковочный станок). Специализированные станки выполняют только один технологический процесс (пример — кривошипные вытяжные). Специальные прессы производят конкретный вид изделий, используя одну технологию.
Принцип работы и устройство прессов различных типов
Любой стандартный штамповочный станок состоит из следующих основных узлов: мотора, передачи, исполнительного механизма. Передача и двигатель вместе составляют «привод». Главная характеристика привода — это вид связи двигателя и исполнительного механизма: механическая или не жесткая (жидкость, газ, пар). Рабочие органы прессов: валки, ползун, траверсы, ролики, бабы.
Кривошипно-шатунный пресс
Привод станка вращается, движение на ползуне преобразуется в возвратно-поступательное. Под действием этого движения при помощи штампа обрабатывается металл. Все детали станка производят из прочной стали и оснащаются ребрами жесткости. Движение ползуна происходит по жесткому графику. Усилие по ползуну достигает 8 тысяч тонн. Кривошипные ковочные установки позволяют ускорить, упростить и удешевить производство деталей, сэкономить до 30% проката. Все кривошипные станки делятся на простые, с двойным и тройным действием.
Кривошипно-шатунный пресс способен выполнять следующие виды работ:
- штамповку в открытых и закрытых матрицах;
- формирование заусенца;
- выдавливание;
- прошивку;
- комбинированную обработку.
Механический пресс воздействует на материал ударом, тогда как гидравлический, прилагая меньшую силу, получает больший эффект. Поэтому вторые используют для изготовления крупных изделий с толстыми стенками.
Гидравлические прессы
Способны проштамповывать поверхность, продавливать и ковать изделия из металла. Они также применяются для переработки металлических отходов. Действие станка основано на увеличении силы давления на металл во множество раз. Пресс представляет собой два сообщающихся цилиндра с водой, между которыми проходит труба. В цилиндрах установлены поршни. Принцип работы пресса основан на законе Паскаля.
Обрабатывает металл горячим способом. Болванка поступает в нагревательный модуль, функционирующий по принципу индукции. Здесь она нагревается, когда металл становится достаточно податливым, подается через конвейер на механизм захвата, подающий заготовку прямо в зону обработки. Ковка или штамповка осуществляется бойками, в процессе заготовка все время крутится, благодаря чему она обрабатывается равномерно со всех сторон. Пресс работает от электромотора, соединенного клиноременной передачей с валами. Они размещены вертикально и направляют движение на шатун и боек, между которыми установлен ползун. Чтобы все движения механизма были синхронными, существуют копирные барабаны. Держатель болванки вращается электромотором посредством червячных передач. Пружинная муфта в нужные моменты притормаживает движение.
Это новейшая разработка, которая только начинает использоваться в промышленности. Рабочий орган станка — сердечник электромагнита, который совершает движения под действием электромагнитного поля. Сердечник двигает ползун или штамп, пружины возвращают ползун в исходное положение. Такие станки отличаются высокой производительностью и экономичностью. На сегодняшний день существуют модели с небольшой амплитудой движения рабочего органа — 10 мм и усилием не более 2,5 тонны.
Работа штамповочного станка черновой обработки в видеоролике: